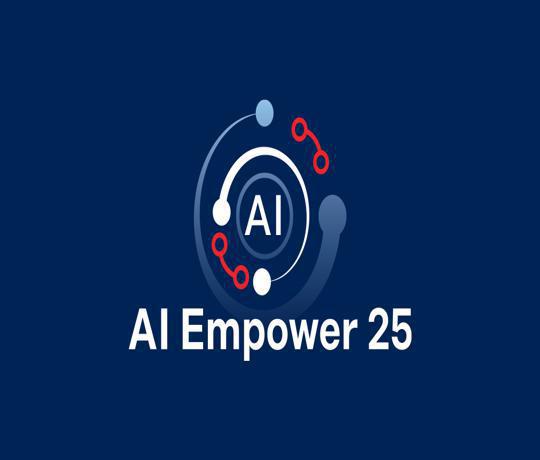
Koenig & Bauer Demonstrates Pioneering Spirit through Compr…
Koenig & Bauer, a globally leading manufacturer of printing presses, has announced the launch of its comprehensive Artificial Intelligence (AI) programme, ‘AI Empower 25’. With this strategic initiative, the company underscores its pioneering spirit and secures its competitiveness through the forward-thinking integration of AI technologies and a unique training approach for its employees.
As part of a groundbreaking partnership with Google, Koenig & Bauer is immediately providing its teams with a range of powerful AI tools. These include the Gemini App as a versatile AI assistant, Gemini Advanced for Workspace for integrated AI assistance directly within Google tools, NotebookLM Plus for specialised knowledge tasks based on internal company documents, and Google Vids for AI-supported video creation. The introduction of these tools, particularly Gemini for Workspace and NotebookLM Plus, marks a decisive step towards a more efficient and productive working environment at Koenig & Bauer.
The core of the ‘AI Empower 25’ programme, however, lies not only in the provision of cutting-edge technologies but much more in the belief in the ability and potential of employees to make optimal use of these technologies. Under the motto ‘The Power Is You!’, Koenig & Bauer is adopting a decentralised training approach. Over the coming months, executives and selected AI Champions from around the world will receive intensive training and will act as multipliers and first points of contact for their colleagues. While the specific training is initially reserved for the AI Champions, the AI tools are already available to all employees to gain early experience and benefit from the advantages of AI in their daily work. Further training opportunities will follow to ensure broad acceptance and utilisation. As an incentive for innovative ideas and outstanding commitment in dealing with AI, the AI Award will be presented in December. This prize aims to honour the creative use of the new tools and the development of solutions to improve daily work.
“With ‘AI Empower 25’, we are once again demonstrating our pioneering spirit,” says Dr Stephen Kimmich, CEO of Koenig & Bauer. “We are convinced that the successful integration of Artificial Intelligence not only increases efficiency and productivity but also sustainably strengthens our company’s innovative power. By actively involving our employees in this change and providing them with targeted training, we ensure that we remain at the forefront of technological development and secure our competitiveness in the long term.”
Koenig & Bauer isn't just boosting its internal AI expertise through the 'AI Empower 25' programme; it's also investing externally in AI-based solutions. Koenig & Bauer Kyana, a business unit spun off from the Group's digital unit on 1 April 2025, focuses on developing digital business models, as well as AI and data-based solutions throughout the entire lifecycle of print products. Its digital product portfolio already includes established solutions like Kyana Assist, the AI-powered expert, and Kyana Data, an intelligent production data analysis tool. This portfolio is continuously being expanded with other pioneering AI and data-based applications to meet customer needs even more precisely and to maximise growth potential in the dynamic market segment. While 'AI Empower 25' focuses on empowering Koenig & Bauer's own employees to boost internal efficiency and productivity, Koenig & Bauer Kyana's products and offerings aim to support customers in the print and packaging industry with innovative digital solutions and optimise their production processes.
With ‘AI Empower 25’, Koenig & Bauer is setting a new standard in the industry and demonstrating how a forward-thinking approach to digitalisation and employee training can pave the way for a successful future.
Recent Comments